ArcelorMittal
In 2024, we successfully completed a large-scale total project for ArcelorMittal: Tankfarm 7.
This project included the entire process from detailed engineering to execution. We provided the piping and support structures. Thanks to our comprehensive approach and close cooperation with the client, we were able to complete the project within the agreed lead time of 35 weeks (and within budget).
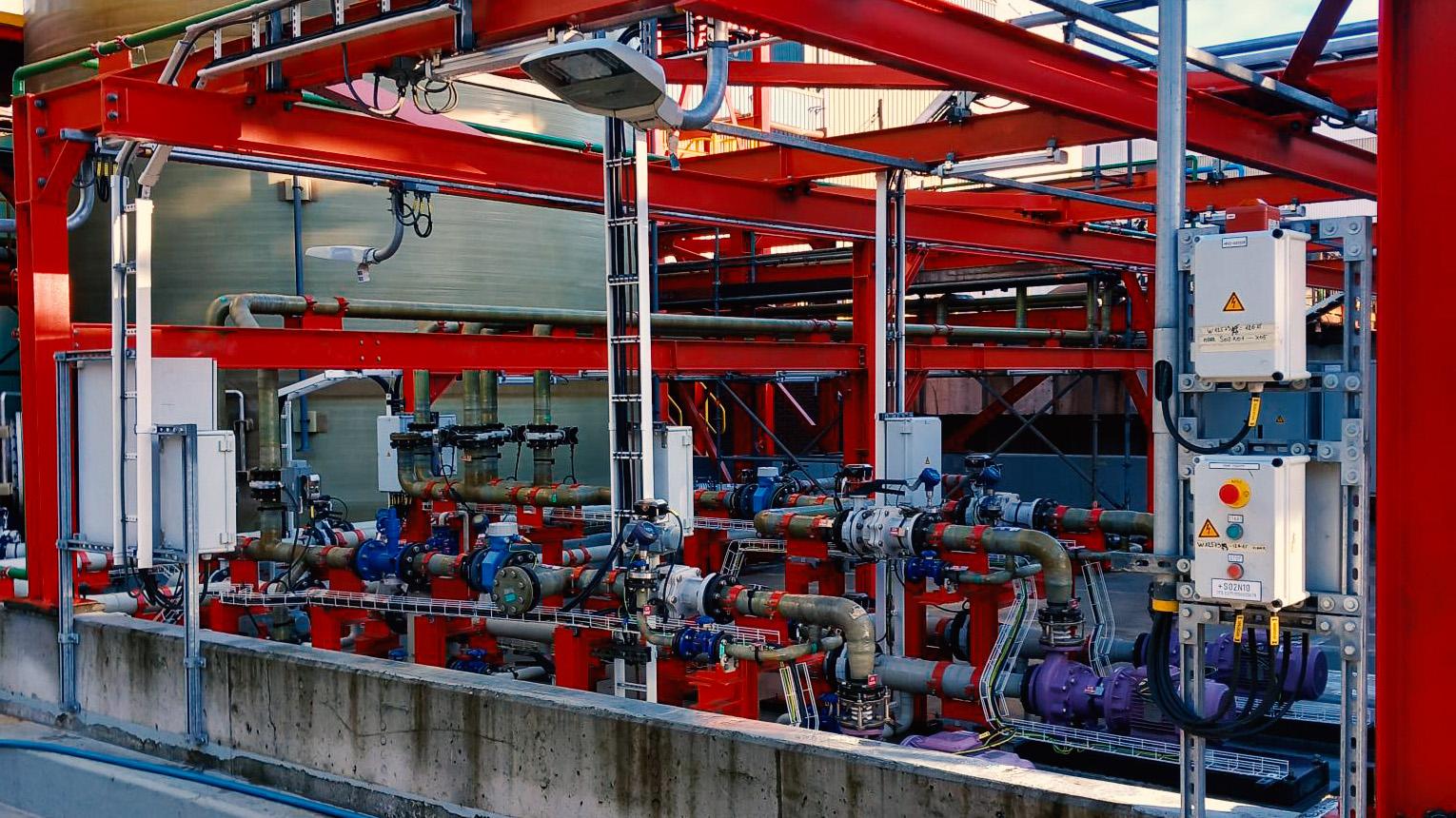
“Completing a total project like this requires not only technical expertise, but also a keen eye for detail and excellent cooperation with the client. Thanks to our innovative approach, including the use of 3D scanning and the application of double-laminated pipes, we delivered a safe, durable, and future-proof result. This approach demonstrates our commitment to quality and customer satisfaction.”
SERVICES
MATERIALS AND TECHNIQUE
A key component of this project was the use of double-laminated piping. This piping consists of a polypropylene (PP) core encased in a fibreglass reinforced (GRP) outer layer. This construction offers an excellent combination of chemical resistance and mechanical strength. The welding process requires precision and is carried out in two steps:
- Mirror welding of polypropylene: This involves heating the ends of the PP pipes and fusing them together.
- Lamination: A fibreglass reinforced layer is applied around the PP pipes for extra strength and durability.
This advanced welding method ensures a robust and leak-free bond, which is essential in installations where chemical resistance and safety are top priorities.
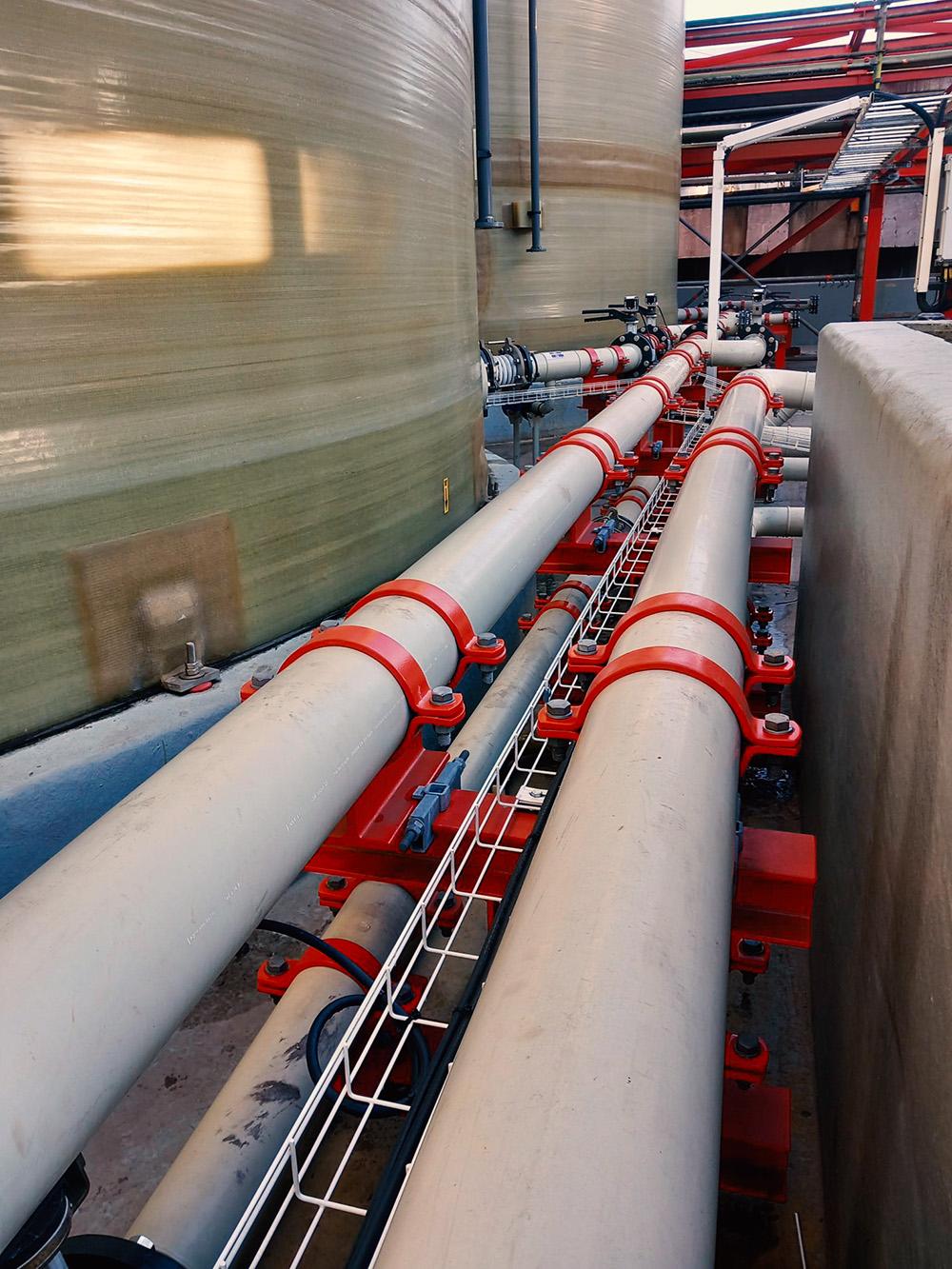
CHALLENGES AND SOLUTIONS
One of the biggest challenges was the limited space within the tank farm, which made positioning piping and supports a complex puzzle. By using advanced 3D scanning and modelling, we were able to simulate the situation in a digital environment, avoid collisions and achieve a seamless installation.
In addition, the use of double-laminated piping placed specific demands on the welding process. By investing in specialised training for our welders and ensuring strict quality control, we guaranteed a flawless execution of the welding and lamination process. This minimised the risk of leaks and guaranteed a durable installation.
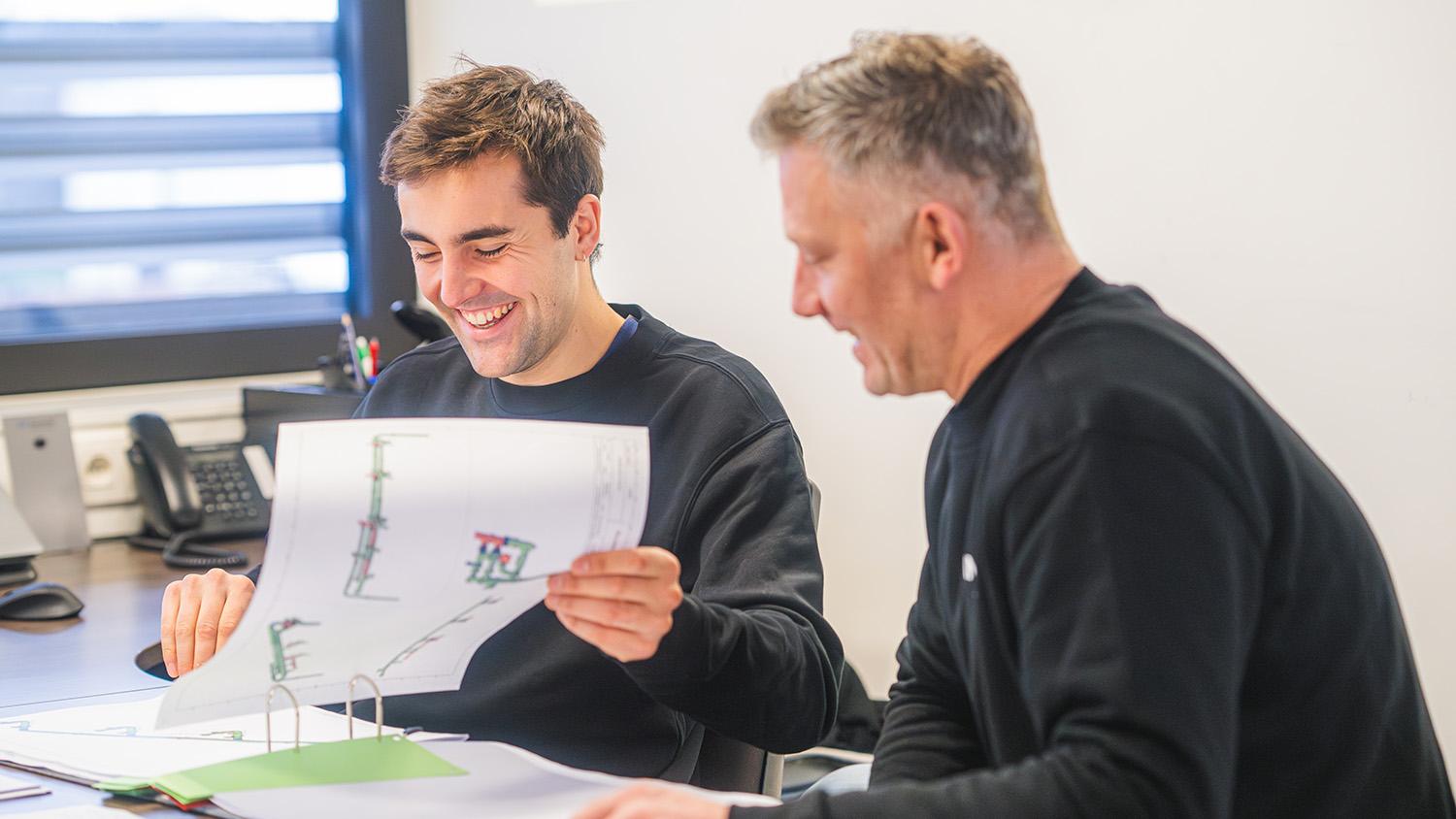
PROJECT RESULT
The successful completion of this project can be attributed to our comprehensive approach, which focused on cooperation, expertise, and accurate planning. With a lead time of 35 weeks and a total of 10,800 hours worked, the project was completed within the agreed schedule and budget. Our approach resulted in a robust and reliable installation that meets the highest safety, quality, and durability standards.
Let’s make your project flow
Need a reliable partner for your piping project? Indinox provides an efficient, hands-on comprehensive approach— from enquiry to execution and follow-up.